SOMANET for
AGV and AMR
THE ALL-IN-ONE SOLUTIONfor AGVs
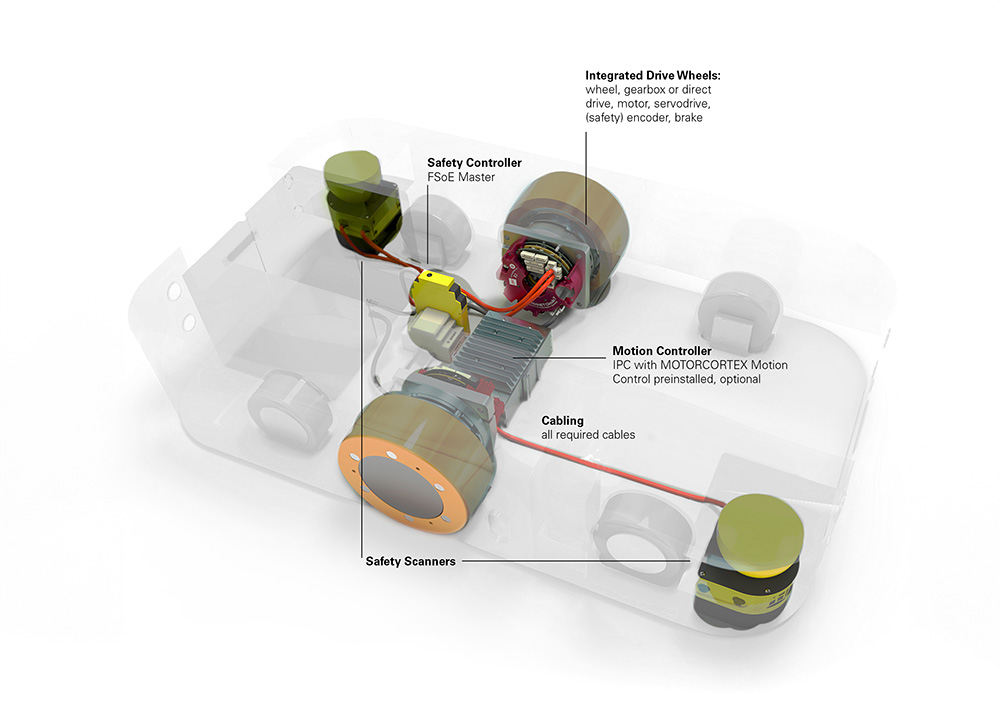
Discover the turnkey solution for AGV and AMR now. A complete kit consisting of integrated drive wheel, safety controller, motion controller IPC, safety scanners and the complete cabling
AGV TURNKEY SOLUTIONMAINTENANCE
ADVANTAGES of the
"NEXT-GEN" AGV
SOMANET solutions for AGV/AMR applications offer many advantages . The All-in-One AGV Axis Solution from Synapticon combines wheels, motor, servo drive, encoder and optional functional safety with an integrated brake in a single unit. This significantly simplifies development, and reduces production effort and costs. Additionally, maintenance is far less complex.
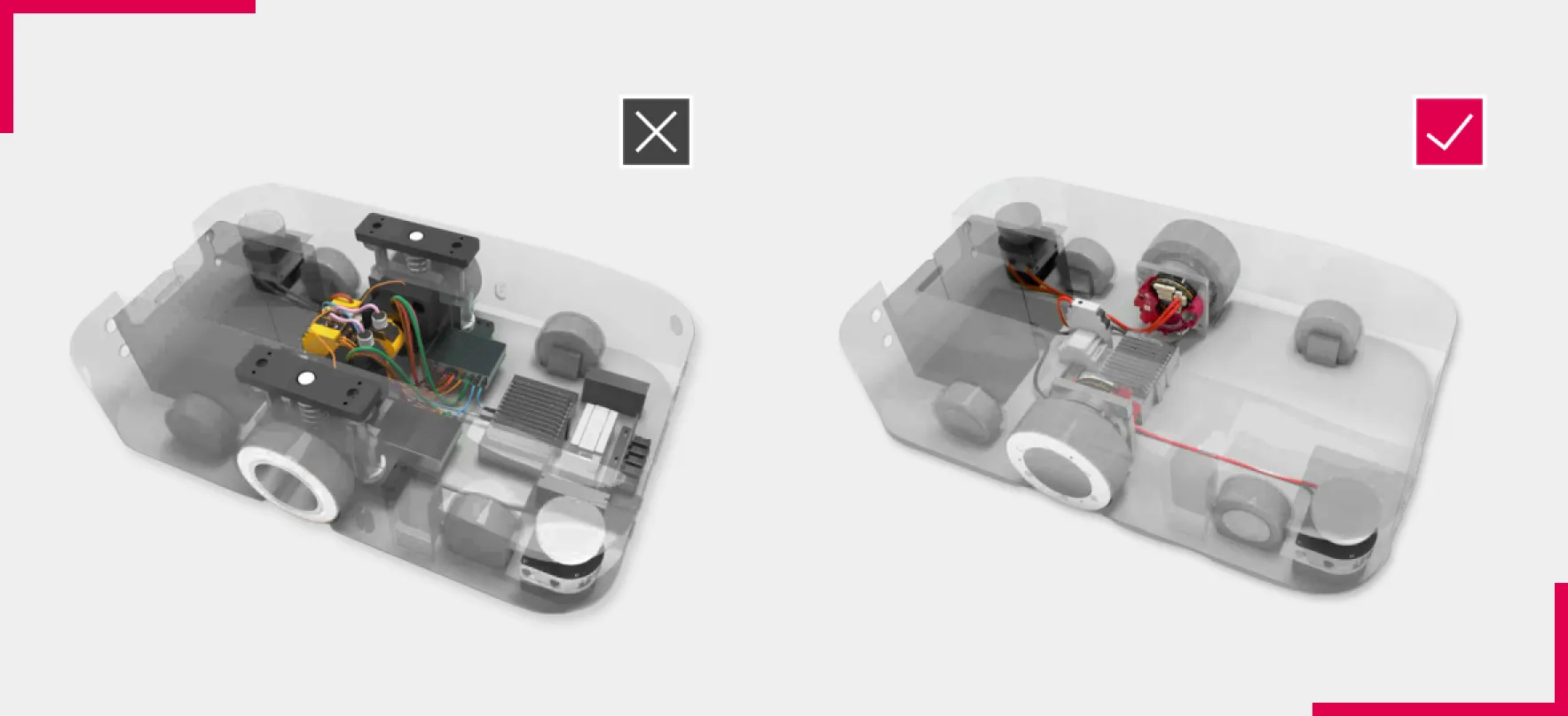
- Reduced complexity of the system
- More space for batteries
- Fast maintenance
- Fewer system failures
- Shorter development time
- Longer running times
- Shorter downtimes
- Fewer components with the same functionality
SIMPLE
CABLE-MANAGEMENT
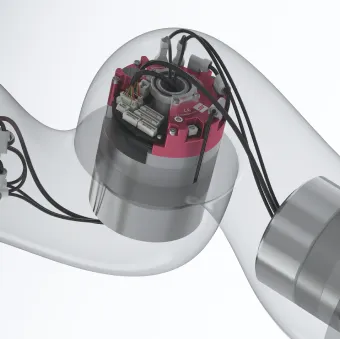
Saves costs and a lot of space inside the AGV.
Safe and reliable environment in the AGV or AMR.
REQUEST A DEMO
INTEGRATED BRAKE SYSTEM
The solenoid actuator is specifically designed for locking rotary motors. When energized, the lock remains retracted and the motor can turn. When de-energized, locking occurs.
This brake system acts like a holding brake and thus prevents any movement of the AGV. This prevents unwanted movements of the AGV and guarantees a safe stop.
CERTIFIED
THE FUTURE FOR REAL HUMAN-ROBOT COLLABORATION is now
STO prevents the trolley from restarting unplanned. STO enables safe working and has a wide range of applications with moving axes.
SBC enables the safe activation of a holding brake. The function is always activated in parallel with STO and used with STO or SS1. This prevents the movement of an axis in a torque-free state.
...
The SS1 function causes the motor to stop quickly and safely, and brings it to a standstill.
The SS2 function switches a motor off quickly and safely. If the motor comes to a standstill, a safe operating stop (SOS) is triggered.
SLS ensures that the drive does not exceed a defined speed limit and triggers an error response if this is exceeded.
The safety function monitors that the drive (and thus the element moved by the drive) does not exceed defined end positions.
Safely limited torque. The SLT function enables the torque to be reduced within a defined time; if the torque exceeds the SLT monitoring limit, the drive reacts with a "safe stop".
via FSoE (7 ms cycle time)
via FSoE (7 ms cycle time)
via FSoE (7 ms cycle time) - when connecting a safe torque sensor to the safe analog input.
via FSoE (7 ms cycle time)
SAFETY FIRST
The optional Safe Motion module for Circulo enables safe motion functions at SIL3, PL-e level via FSoE (FailSafe over EtherCAT). Realize your application in accordance with ISO/TS 15066.
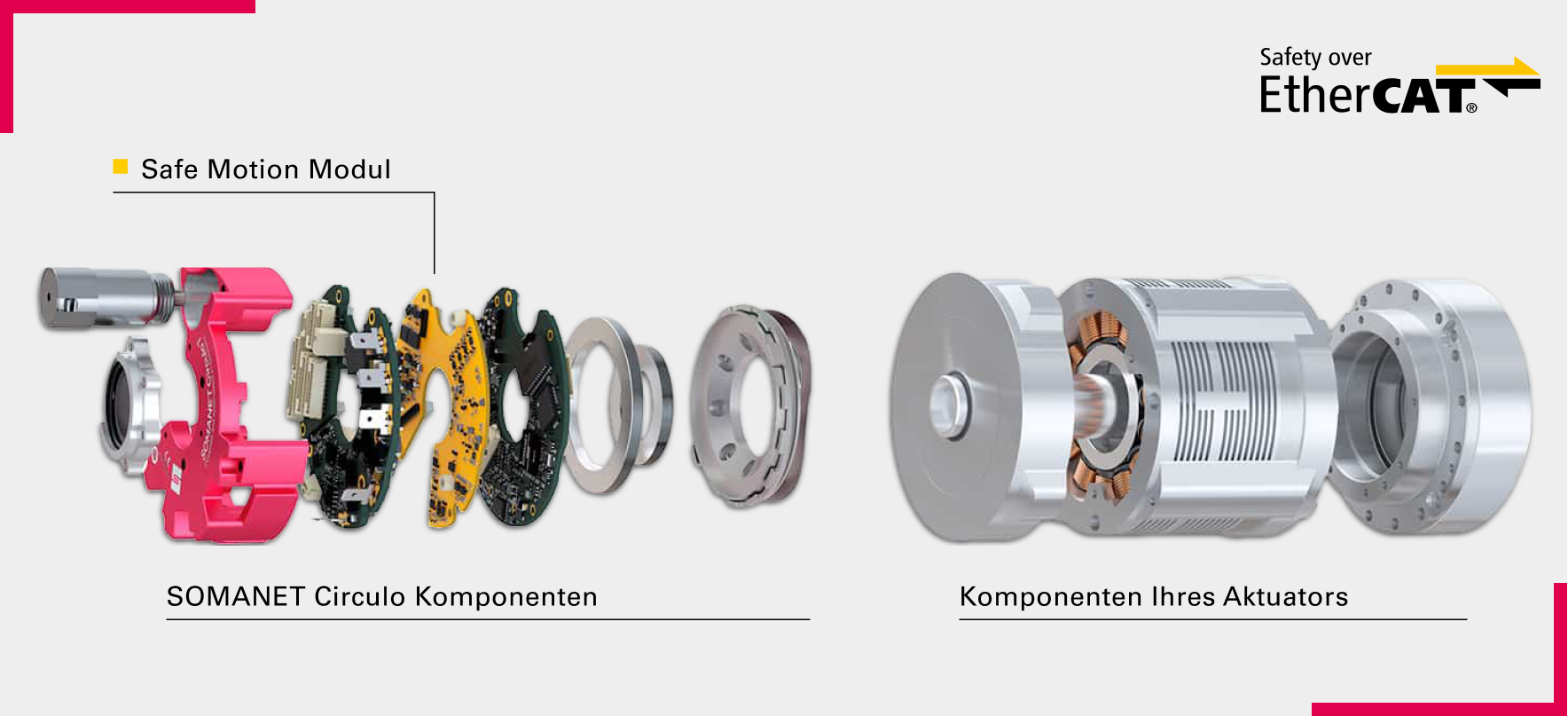
FEATURED CUSTOMER PRODUCTS
Talk to us, we will be happy to explain more details.