ROBOTIC ARMS
AND COBOTS
SOMANET Circulo is the perfect all-in-one
solution for collaborative robots
SOMANET Circulo enables the highest performance in motion control, best UX, supported integration and frameless EVM. The Circulo is safety certified (SIL3 PLe), and stands for our principle of absolute safety in robots and cobots. Additionally, check-out our Featured Products, in which our SOMANET solutions have (long) been successfully used.
- Compact dual encoder arrangement
- Alignment of the encoder scanning head
- Thermal management
- Hollow shaft (20 mm and 40 mm) with support bearing
- Addition of customized parts, such as third-party cable retention system encoder or IMU
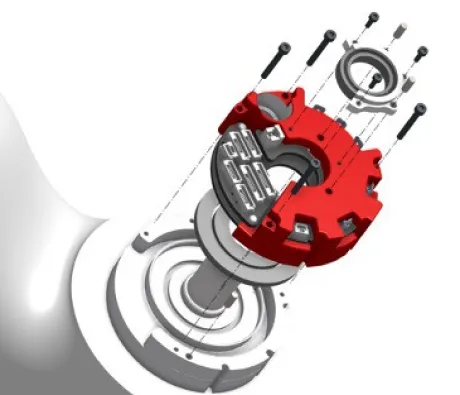
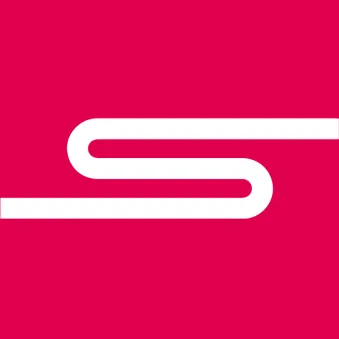
SIMPLE
CABLE MANAGEMENT
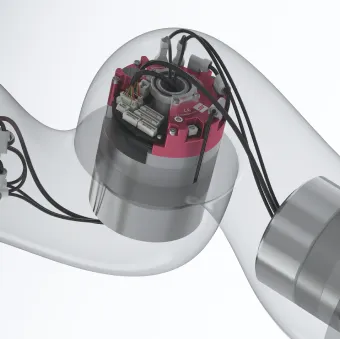
Saves costs and a lot of space inside the robot.
Safe and reliable environment in the robot or cobot.
REQUEST A DEMO
CERTIFIED
THE FUTURE FOR REAL HUMAN-ROBOT COLLABORATION is now
STO prevents the trolley from restarting unplanned. STO enables safe working and has a wide range of applications with moving axes.
SBC enables the safe activation of a holding brake. The function is always activated in parallel with STO and used with STO or SS1. This prevents the movement of an axis in a torque-free state.
...
The SS1 function causes the motor to stop quickly and safely, and brings it to a standstill.
The SS2 function switches a motor off quickly and safely. If the motor comes to a standstill, a safe operating stop (SOS) is triggered.
SLS ensures that the drive does not exceed a defined speed limit and triggers an error response if this is exceeded.
The safety function monitors that the drive (and thus the element moved by the drive) does not exceed defined end positions.
Safely limited torque. The SLT function enables the torque to be reduced within a defined time; if the torque exceeds the SLT monitoring limit, the drive reacts with a "safe stop".
via FSoE (7 ms cycle time)
via FSoE (7 ms cycle time)
via FSoE (7 ms cycle time) - when connecting a safe torque sensor to the safe analog input.
via FSoE (7 ms cycle time)
SAFETY FIRST
The optional Safe Motion module for Circulo enables safe motion functions at SIL3, PL-e level via FSoE (FailSafe over EtherCAT). Realize your application in accordance with ISO/TS 15066.
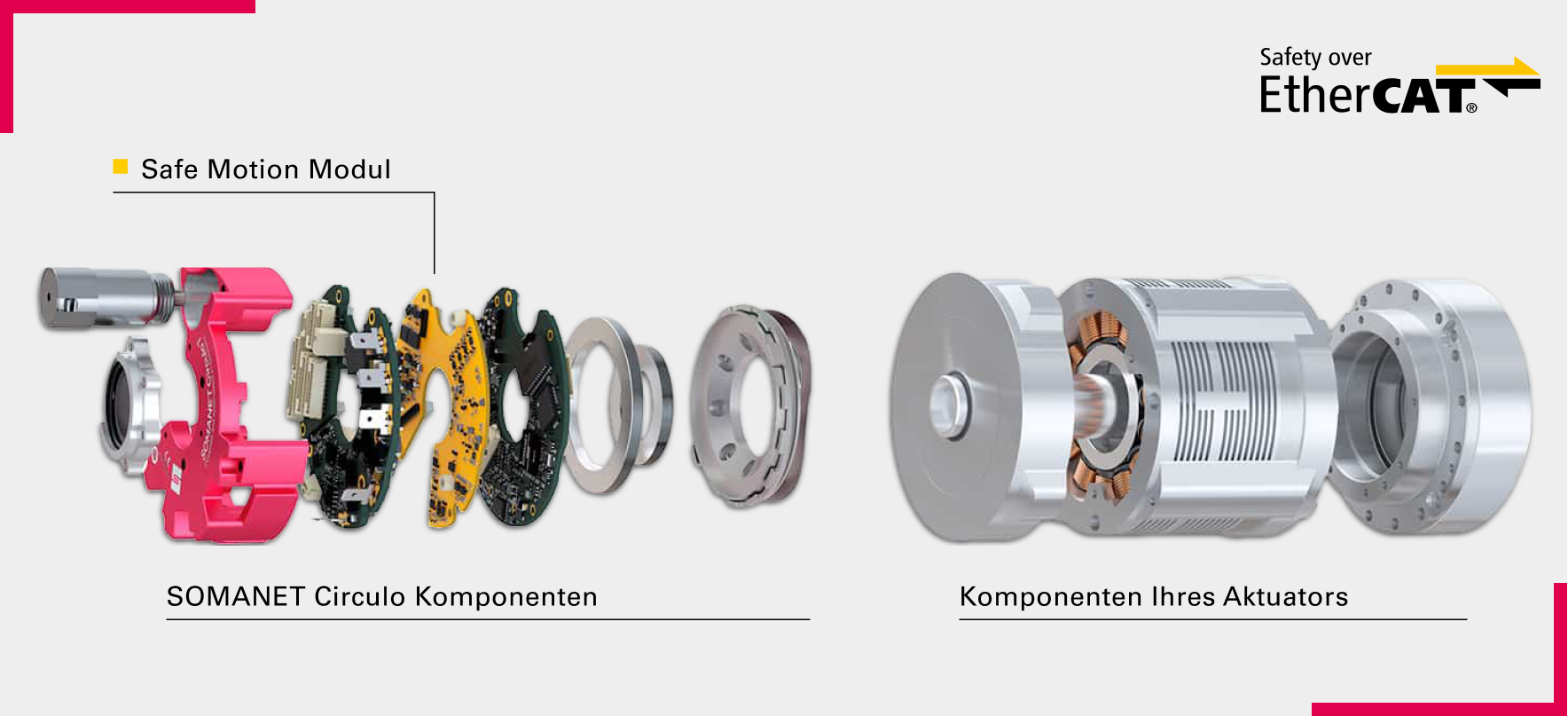
FEATURED CUSTOMER PRODUCTS
Talk to us, we will be happy to explain more details.
SUMITOMO TUAKA DRIVE
- 3 sizes
- High rigidity
- Lost Motion 1.0 arcmin
- Transmission error 0.75 arcmin
- Max. Output speed up to 123 rpm
- Supply voltage 48 V
Absolute security
Additional safety functions are available with a safety level of up to SIL3 PLe
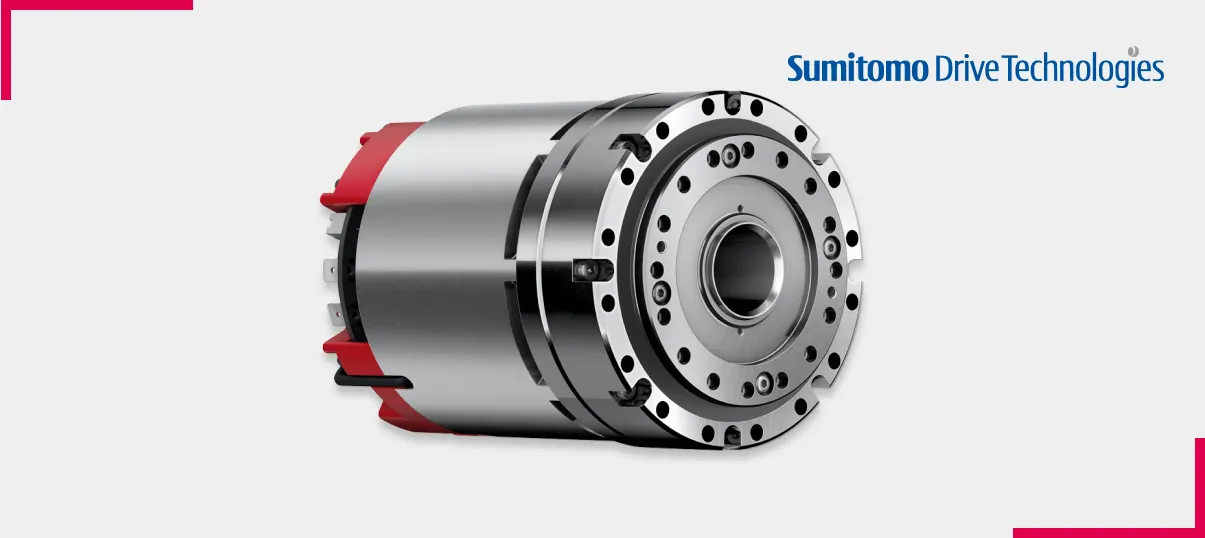
SCHAEFFLER MODULAR PRECISION DRIVE SYSTEM
The basic version is available with High Torque RT1 or Standard Torque RT2 precision shaft gearboxes and a motor matched to the gearbox performance. Options: Hall sensor, temperature sensor and brake ready for operation in one housing.
Ready-to-install drive with absolute encoder. There are two solutions to select from: single-sided for an encoder at the gearbox input, or double-sided for encoders at the gearbox input and output.
The Premium package includes an integrated drive controller. The drive is preconfigured with the appropriate parameter set and can be placed into operation immediately after connecting to the power supply and control system.
Digital services included - possibly in conjunction with additional sensors, such as vibration sensors. Based on operating data, questions about the current and future condition of the drivetrain or process can be answered.
CENTRAL COMPONENTS
The Modular Precision Drive system has two precision shaft gearbox series: High Torque RT1 and Standard Torque RT2, with their wide range of variants.
.webp)
SENSODRIVE SENSOJOINT
From the Sensodrive torque sensor to the Somanet Circulo Servo
Drive and the Harmonic Drive® gearbox - only market-leading components that are perfectly matched to each other are used in the SensoJoint
drive modules.
.
The ready-to-install SensoJoints combine all drive components in
a compact, lightweight design. With five sizes and flexible
interfaces, they can be installed out of the box in almost any robotics solution
.
Thanks to extensive integrated safety functions, SensoJoints meet the
SIL3/PLe requirements and are already fully safety-certified.*
Time and costs for lengthy certification processes
are eliminated.
Whether sensitivity, precision, performance or safety -
SensoJoints regularly set new standards.
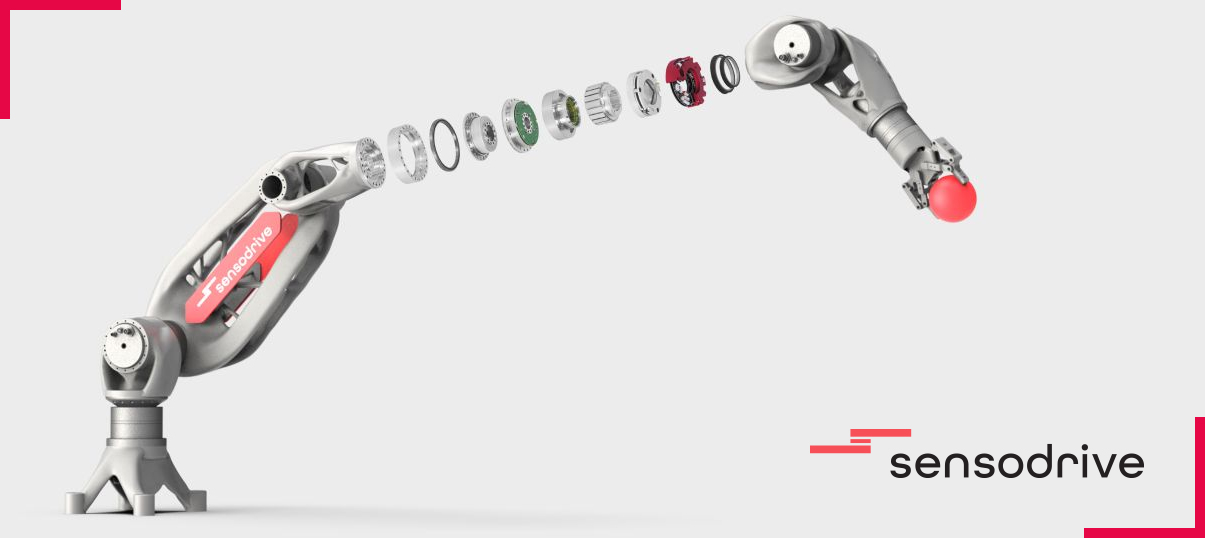
SERVONEERING
Solution: In our collaboration, Servoneering used our advanced motor controllers to speed up development and make the process more efficient than ever before.
Impact: This strategic partnership reduced the development time from 2-3 years to just 1-1.5 years. This drastic reduction in time leads to a faster time to market and significant cost savings, especially in high-volume production. It represents a major step forward in terms of efficiency and innovation in robot production.
STRONGLY REDUCED DEVELOPMENT TIME
Find out here how our customer Servoneering drastically shortens the development time of a robot drive, making it significantly cheaper and faster to market.