SOMANET
NODE
Highest current density
for maximum power
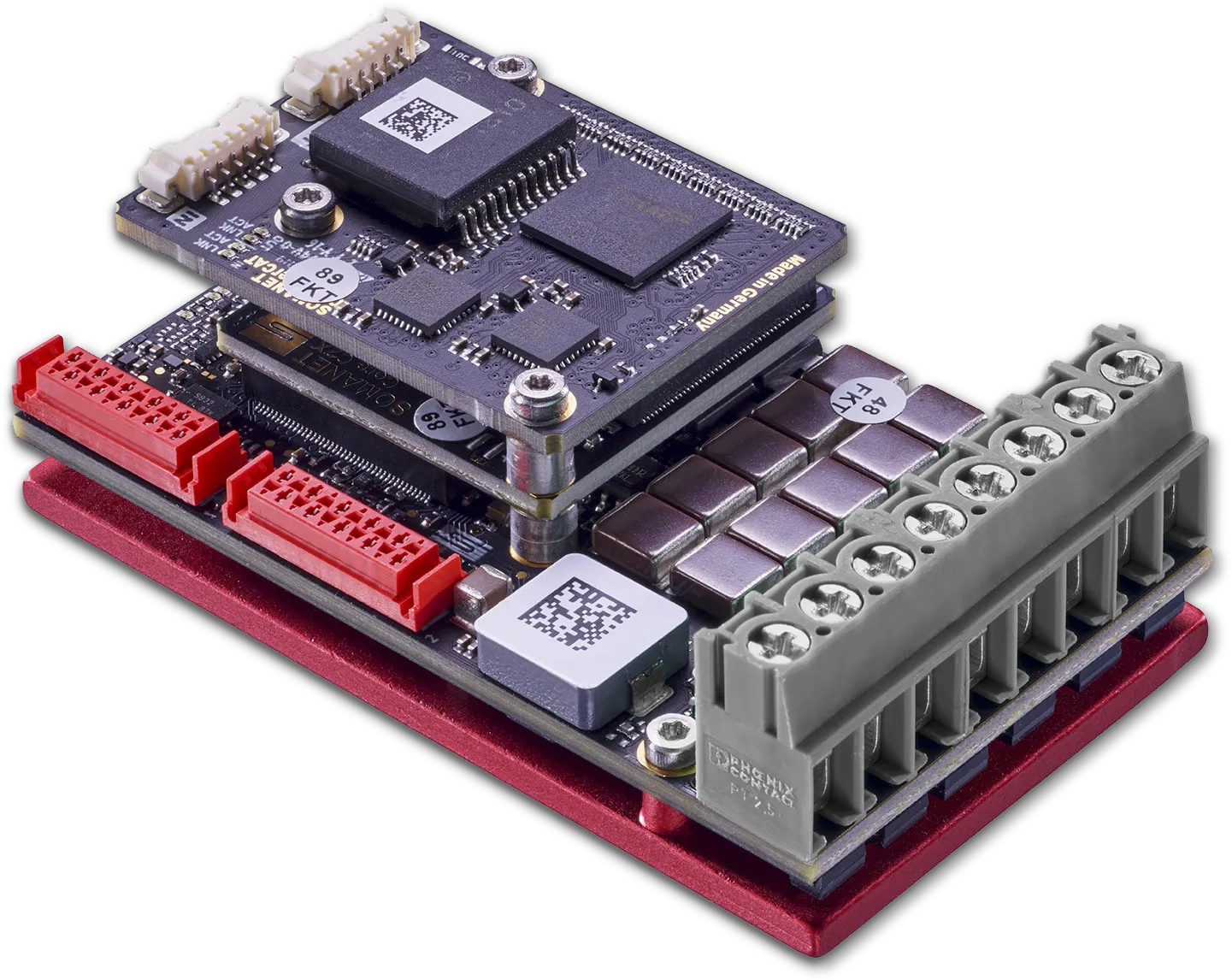
The compact and efficient SOMANET Nodes servo drives outperform comparable products many times over in terms of power density. They support all PMSM, synchronous AC and BLDC motors up to 60 V and 100 A / 66 A_rms and have an EtherCAT interface with CiA DS 402 protocol.
SOMANET nodes increase the performance of motors and gearboxes in your drive control systems thanks to intelligent algorithms. They enable precise and at the same time fast movements of your robots and can precisely regulate the position, speed and acceleration of a robot arm.
All functions of the SOMANET Node series are compatible with OBLAC Tools, an easy-to-use yet powerful tool suite for commissioning and motion tuning.
BOOK PRODUCT DEMOSOMANET nodes increase the performance of motors and gearboxes in your drive control systems thanks to intelligent algorithms. They enable precise and at the same time fast movements of your robots and can precisely regulate the position, speed and acceleration of a robot arm.
All functions of the SOMANET Node series are compatible with OBLAC Tools, an easy-to-use yet powerful tool suite for commissioning and motion tuning.
Maximum power
for servo drives
HIGHEST CURRENT DENSITY ON THE MARKET
Unique performance with minimal heat generation.
UNSURPASSED INTEGRATION SUPPORT
The maximum power output is usually much higher thanks to optimum integration.
ADVANCED INTERFERENCE COMPENSATION
Detects sensor noise, non-linearities in the motor and gearbox as well as cogging torque.
Frameless EMC
Electromagnetic compatibility, the ability of a technical device not to interfere with other devices through unwanted electrical or electromagnetic effects or to be interfered with by other devices.
CERTIFIED FUNCTIONAL SAFETY
Has TÜV-certified STO and SBC functions at SIL3 PLe level.
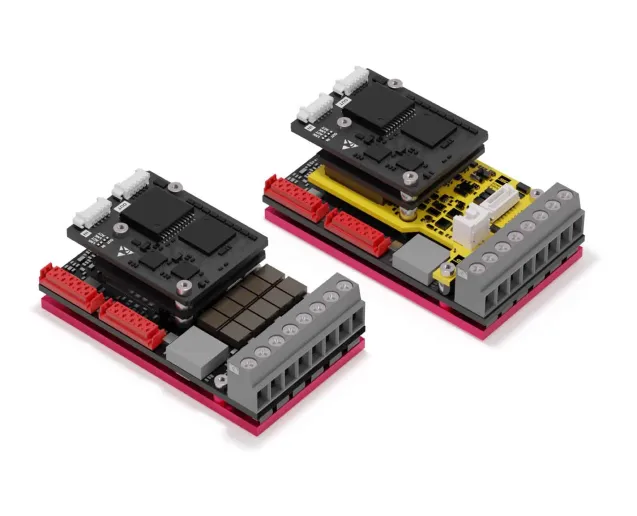
ULTRA COMPACT
Elimination of the control cabinet, massive cable savings and significantly reduced complexity of the application.
Versatile
3 modules of a SOMANET node in several performance levels as well as basic safety functions.

EFFICIENT
Smooth-running drives with low thermal output and very high motion control performance.
Servo drive in 3 modules
A SOMANET Node consists of three modules: communication (Com), processor (Core) and drive module. Several standard options are available for each of these modules. We can also develop customer-specific modules for you on request.
SOMANET Node Safety also has TÜV-certified STO and SBC functions at SIL3 PLe level.
SOMANET Node Safety also has TÜV-certified STO and SBC functions at SIL3 PLe level.
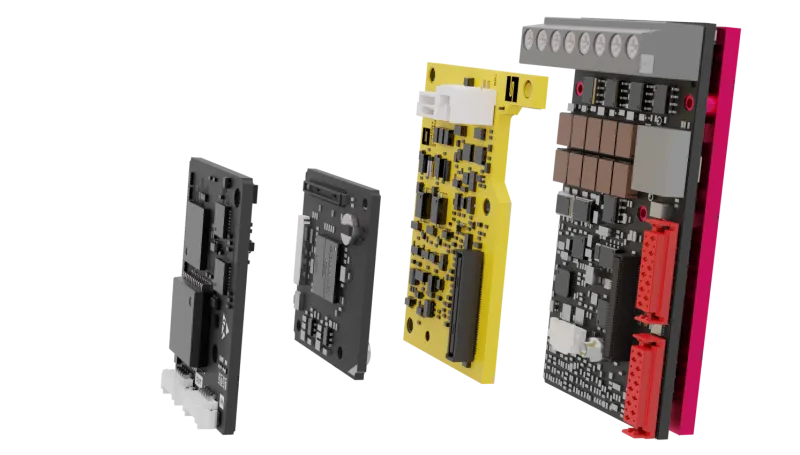

- Reduces the number of cables from 100 to 6
- Simplifies your production design
- Reduces the costs of your robot or machine systems
- Can be expanded with additional safety functions or sensors
INTELLIGENT ALGORITHMS
for maximum EFFICIENCY
Experience motor phase monitoring at high speed and high resolution. This is how motion control of the future will work. The SOMANET software stack offers a model-predictive field-oriented control approach - Model Predicitve Deadbeat Control.
Thanks to this technology, you can achieve perfectly smooth and quiet running drives with low heat dissipation.
Thanks to this technology, you can achieve perfectly smooth and quiet running drives with low heat dissipation.
PERMANENT CONTROL
Consistently calculates the processes in the connected motor.
FLEXIBLE RESPONSE
Can spontaneously select from a range of control strategies.
MAXIMUM ADAPTABILITY
Adapts to the current load situation.
OPTIMUM MOTOR PHASE CONTROL
Reacts to the exact motor geometry.
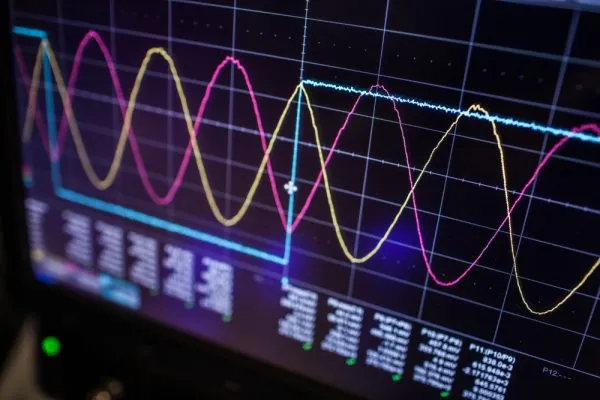
SMALL TENSION
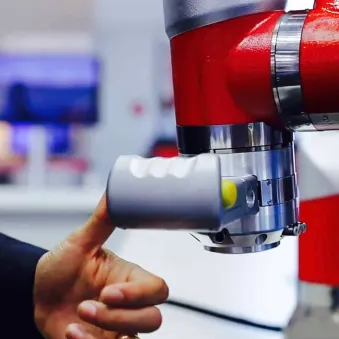
Safe current takes precedence over high current. This is the only way for collaborative robot arms to work intrinsically safe.
Synapticon's frequency inverters work with the most modern power semiconductors on the market.
SOMANET NODES FOR FUTURE-ORIENTED ROBOTICS
With SOMANET nodes, you can realize a simpler product design. Experience maximum performance with the highest possible current density. Save time and costs.
MORE INTELLIGENCE
IN SERVO DRIVES
Synapticon's drives can communicate with a large number of feedback encoders, torque and force sensors. The Synapticon nodes respond to touch-sensitive skins and interpret LiDAR data (customized solutions).
Our servo drive systems can be combined locally with your own software. This allows you to implement reflexes based on sensor signals and other customer-specific algorithms directly on the drive.
Our servo drive systems can be combined locally with your own software. This allows you to implement reflexes based on sensor signals and other customer-specific algorithms directly on the drive.
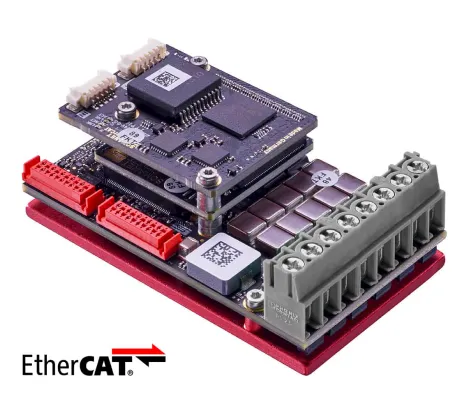
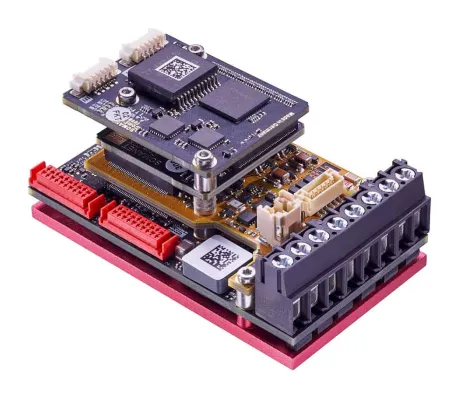
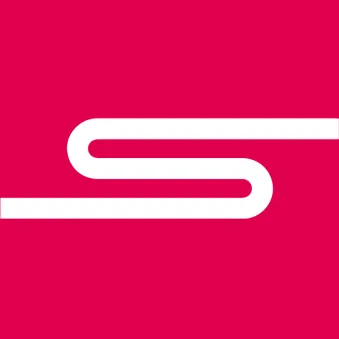
START WITH AN EVALUATION KIT
The easiest way to evaluate SOMANET servo drives.
Test the SOMANET nodes with permanent magnet synchronous motors (PMSM/BLDC) of various sizes up to 2000 W (48 V / 66 Arms) and integrate them as slaves into your EtherCAT system.
Test the SOMANET nodes with permanent magnet synchronous motors (PMSM/BLDC) of various sizes up to 2000 W (48 V / 66 Arms) and integrate them as slaves into your EtherCAT system.
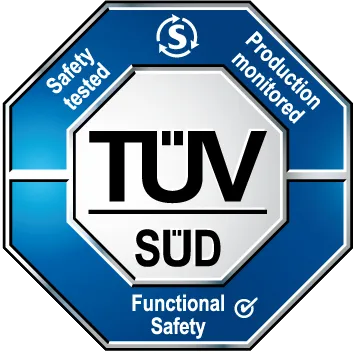
The kit contains:
- A SOMANET Node with the desired rated power (20 - 100 A)
- Cables
- A handy box
- One OBLAC Drive Box (optional)
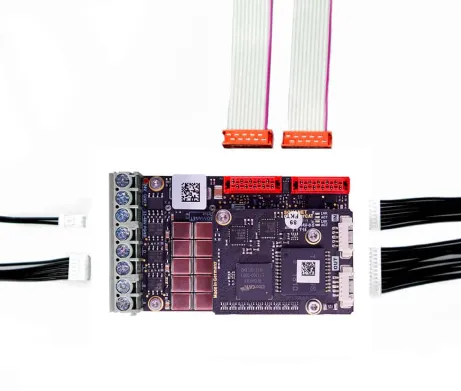
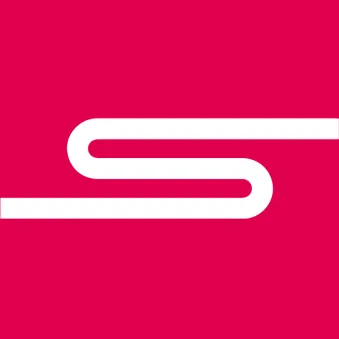
INTEGRATION into motion control systems
Servo drives enable robots to perform precise and fast movements. This is why they are used in many sectors, such as in the automotive, electronics and packaging industries.
OBLAC CONFIGURATIONS
AND TUNING TOOL
Optimize and commission the Synapticon SOMANET nodes with our OBLAC Drive Tools. Our servo drives work with permanent magnet synchronous motors, AC motors or brushless DC motors up to 60 V rated voltage from any manufacturer.
Synapticon's OBLAC Drives Tools facilitates the configuration and optimization of a SOMANET Node for the control of PMSM, synchronous AC and BLDC motors up to 60 V and 100 A / 66 Arms from any manufacturer and feedback sensor.
Synapticon's OBLAC Drives Tools facilitates the configuration and optimization of a SOMANET Node for the control of PMSM, synchronous AC and BLDC motors up to 60 V and 100 A / 66 Arms from any manufacturer and feedback sensor.
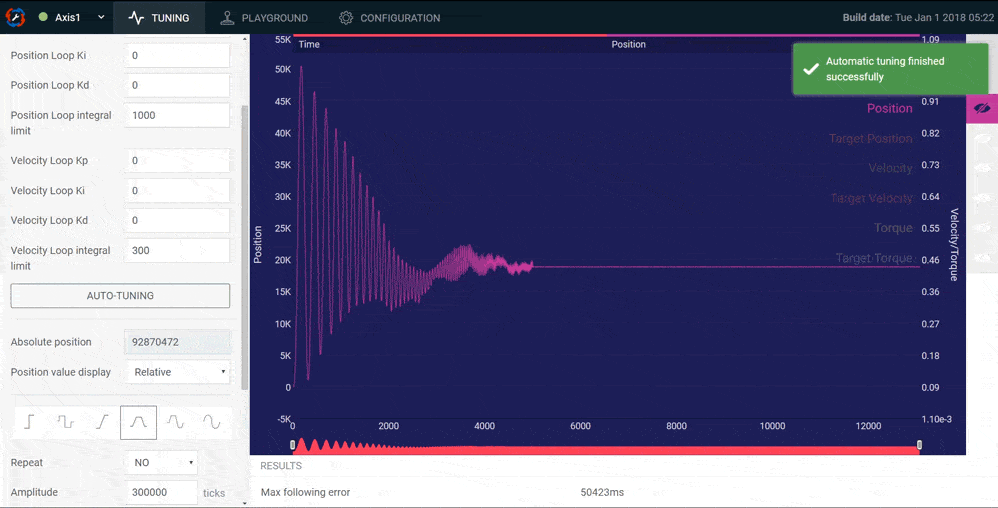
ANY QUESTIONS?
We'll be happy to advise you on Circulo's usage. Talk to us about your project at any stage of its development.