SOMANET
SAFE MOTION
MORE SAFETY WITH
DRIVE CONTROLS
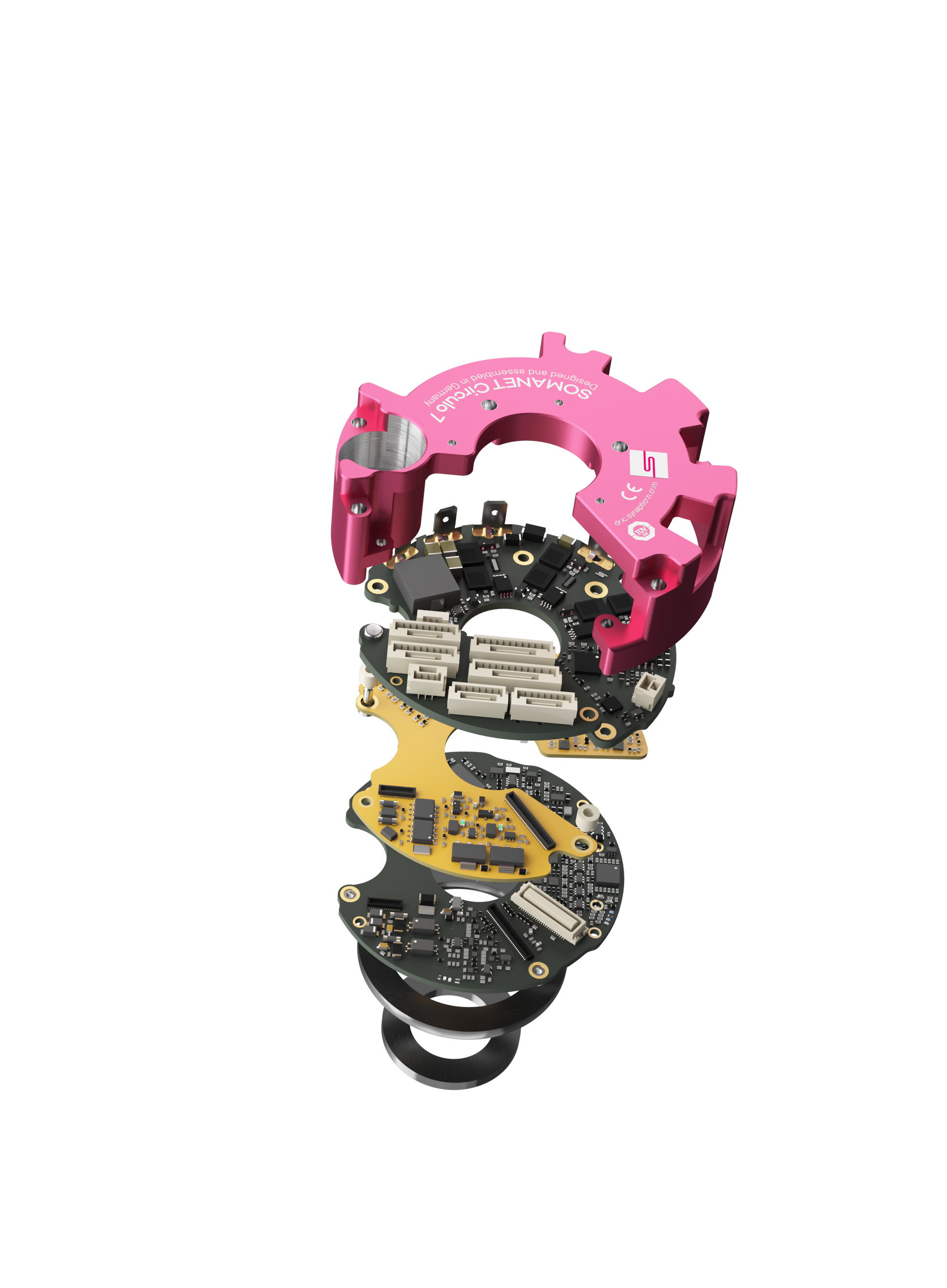
CERTIFIED
SOMANET Safe Motion is physically mounted between the processor module and the drive module. This allows the safety extension to generate and receive safety-critical signals without the need to modify the existing hardware or perform complex cabling of the solution. SOMANET Safe Motion offers safety functions such as STO, SBC, SS1, SS2, SLS, SLP, SLT, all of which are available via FSoE or I/O.
Downloads
ETHERCAT CONFORMANCE
CERTIFIED
THE FUTURE OF TRUE HUMAN-ROBOT COLLABORATION
STO prevents the trolley from restarting unplanned. STO enables safe working and has a wide range of applications with moving axes.
SBC enables the safe activation of a holding brake. The function is always activated in parallel with STO and used with STO or SS1. This prevents the movement of an axis in a torque-free state.
...
The SS1 function causes the motor to stop quickly and safely, and brings it to a standstill.
The SS2 function switches a motor off quickly and safely. If the motor comes to a standstill, a safe operating stop (SOS) is triggered.
SLS ensures that the drive does not exceed a defined speed limit and triggers an error response if this is exceeded.
The safety function monitors that the drive (and thus the element moved by the drive) does not exceed defined end positions.
Safely limited torque. The SLT function enables the torque to be reduced within a defined time; if the torque exceeds the SLT monitoring limit, the drive reacts with a "safe stop".
via FSoE (7 ms cycle time)
via FSoE (7 ms cycle time)
via FSoE (7 ms cycle time) - when connecting a safe torque sensor to the safe analog input.
via FSoE (7 ms cycle time)
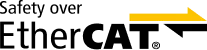
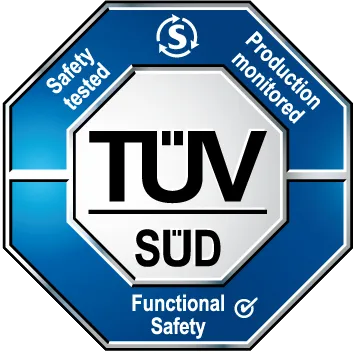
SAFETY FIRST
The optional Safe Motion module for Circulo enables safe motion functions at SIL3, PL-e level via FSoE (FailSafe over EtherCAT). Realize your application in accordance with ISO/TS 15066.
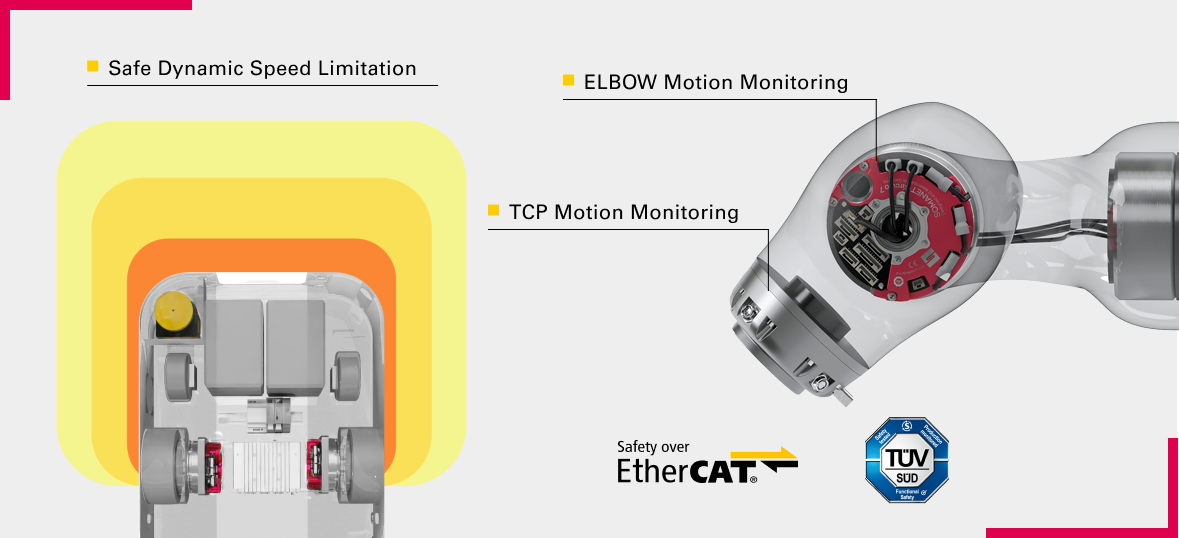
FSoE communiCation
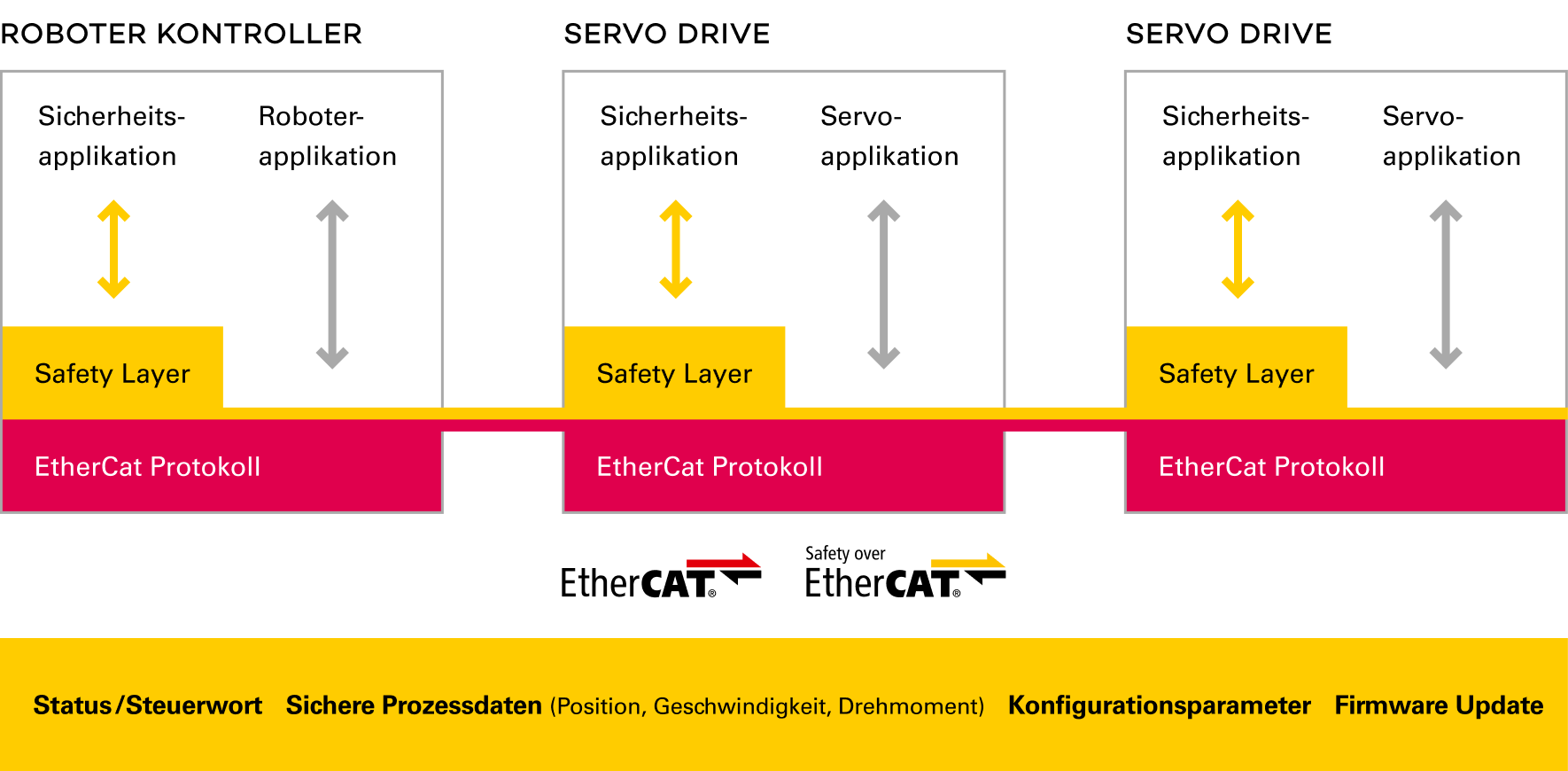
SOMANET Integrated Brake System
- The motor speed is reduced to a low level before the brake engages.
- The brake prevents the motor from rotating unintentionally (e.g., in the event of a power failure).
- In this way, the servo drive prevents unwanted contact with the workpiece being processed or between the robot and human.
APPLICATIONS
SOMANET SAFE MOTION
This requires a new level of intrinsic functional safety for robots. You benefit from advanced safety concepts, especially when production space is limited. Thanks to SOMANET Safe Motion, you no longer need robot cages.
And as a result of safe and secure motion control, system designs can now be realized that allow maintenance procedures to be carried out during operation. Interrupting productivity is "old school". Reducing total cost of ownership is the new deal.
DO YOU HAVE ANY QUESTIONS?
Talk to us about your project at any stage of development.